With the gradual upgrading of the automotive consumer market and the increasingly fierce competition, auto and component manufacturers are faced with two-way pressures of quality improvement and cost reduction. How to effectively ensure the processing quality and precision of auto parts, and continuously improve processing on this basis. Efficiency, shortening the production cost of a single product, has become the focus of current automotive and component manufacturing companies. Especially for engine manufacturing, due to its high-volume, high-precision, high-quality, high-stability processing characteristics, the engine shop must be continuously improved in efficiency to cope with the beat requirements.
Jianghuai Automobile is the leader among domestic brands. Its core engine 1.5TGDI engine is the first domestically developed, mature and mass-produced model. It integrates internationally advanced direct injection, exhaust turbocharged and dual variable. Valve timing, integrated intercooler plastic intake manifold and oil and gas separation integrated cylinder head cover, silent chain drive, breaking link and many other advanced technologies, with high power, high quality, low fuel consumption, Low emission, light weight and other characteristics, compared with the ordinary engine, its fuel consumption can be reduced by up to 30%, which can save 20% of the vehicle fuel, achieving a perfect integration of strong power and ultra-low fuel consumption.
Meet beat and efficiency requirements
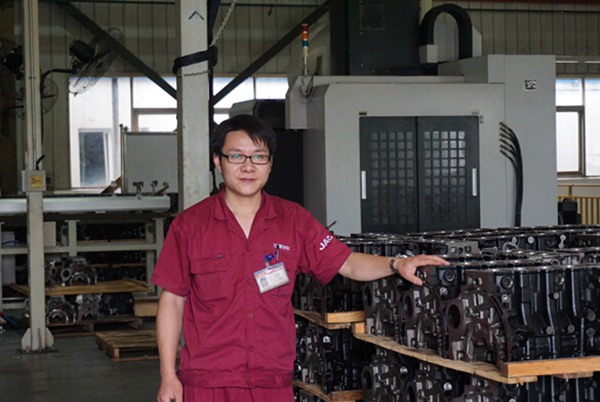
Figure 1. Ren Jianju, workshop director of Hefei Jianghuai Foundry Co., Ltd.
"These are mainly for the JAC Ruifeng S5. Its advantages are low speed, high torque, high speed and high power, which makes the vehicle start faster and more powerful. Usually we have two shifts and efficient production. Faced with the cylinder block of the 1.5TGDI turbocharged direct injection engine that is waiting to enter the next process in the processing workshop, Ren Jianju, Hefei Jianghuai Foundry Co., Ltd. (hereinafter referred to as Jianghuai Foundry, is the controlling subsidiary of Jianghuai Automobile Co., Ltd.) The company's workshop director said, “On the one hand, the Group continuously optimizes the process and reduces the cycle from the adjustment of the process; on the other hand, it requires the work of reducing the cost per piece, and it is beneficial from the cutting process. For us, It is a challenge and an opportunity."
The main business of JAC Foundry is to provide casting products for Jianghuai Automobile Group. After the adjustment of the process of the engine plant of the same group, the machining shop of Jianghuai Foundry undertakes the processing tasks of the cylinder block, mainly focusing on the semi-finishing of the cylinder block. And the finishing process of drilling to achieve more demanding processing beats. According to the introduction, according to the requirements of the Group's high-efficiency production, the cycle requirement for the whole cylinder processing is 2.5~3 minutes. However, due to the processing of the cylinder hole, the overall beat is difficult to achieve the above goal and will be extended to 5~6 minutes. Now, through the process improvement, the casting company completes the hole processing process, and the cycle of the overall cylinder processing can be shortened to 2 minutes and 05 seconds, which is very fast in the same industry.
1 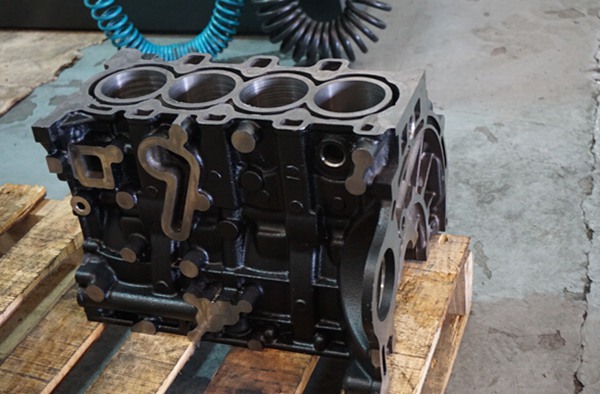
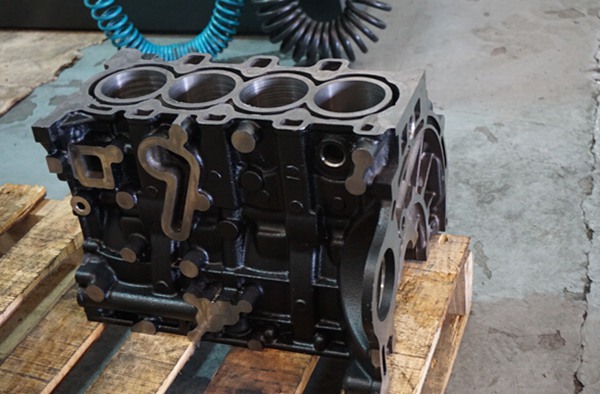
1 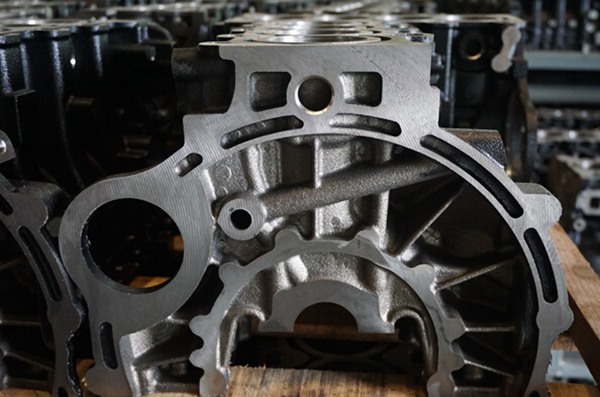
Figure 2. The cylinder block of a 1.5TGDI turbocharged direct injection engine that is waiting to enter the next process in the shop.
The comparison proves that under the same processing efficiency, the life of Walter tool is higher, and the seismic resistance of the tool body is improved.
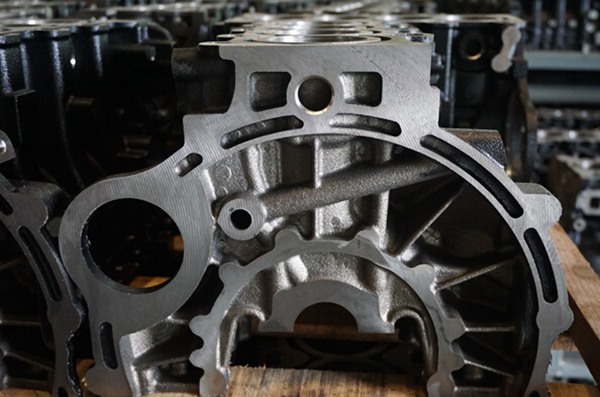
Figure 2. The cylinder block of a 1.5TGDI turbocharged direct injection engine that is waiting to enter the next process in the shop.
The comparison proves that under the same processing efficiency, the life of Walter tool is higher, and the seismic resistance of the tool body is improved.
“When this process was previously processed by the engine company of the group company, it not only could not meet the processing tempo of the whole production line, but also the cost was high. After transferring to the foundry company, the workshop established a professional processing line, and it was also more rigorous when selecting the tool. Comparison," said the director. Due to the mass production, an unexpected event may result in product scrapping or even affecting the tempo of the entire production line, so only tools with better stability can be selected. At present, Jianghuai foundry processing workshops all use imported advanced cutting tools. In order to ensure the production capacity, the principle of high durability, high cutting efficiency and low cost of use is strictly followed in the selection of tools, and the most representative of Walter tools is finally determined. Product range: Walter Titex deep hole drill, Walter BLAXXTM and Tiger·tec® tiger blades.
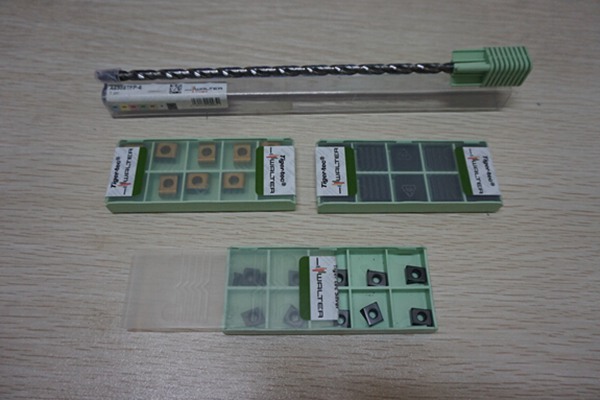
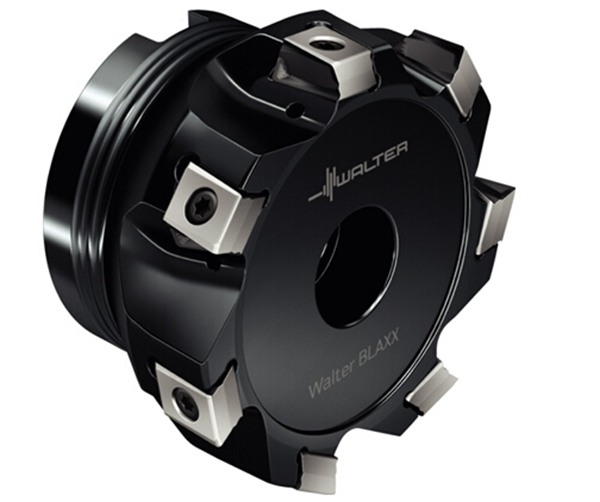
Figure 3. The three most representative product lines of Walter knives are used in JAC Casting:
Walter Titex XD deep hole drill, Walter BLAXXTM (Black Front) and Tiger·tec® Tiger Blade.
Director Ren explained: "We have known for a long time that Walter is the leading tool brand in the world. There are many successful applications in the automotive engine industry, and there are a lot of knives in the brother company that use Walter products, and the reputation is very good. After using the Walter tool in batches, the results really made us very satisfied."
In terms of hole processing that has the greatest impact on the beat, Jianghuai Casting uses the Walter-Texex Alpha 4 XD series of high-efficiency solid carbide internal deep-deep drills (XD deep hole drills). The drill diameter ranges from 3 to 20mm, with a drilling depth of 70 x Dc, ensures maximum process reliability without the need for retraction. The polished chip flutes ensure reliable chip evacuation during deep hole machining, ensuring process quality. Since the drill has four land belts, it has excellent performance in processing oblique outlets and through holes, and is widely used in the automotive industry and general machinery industry. In addition, in order to meet the efficiency requirements of modern machining, Walter Titex XD drills have excellent performance and advanced coatings, which is up to 10 times more efficient than single-blade gun drills.
The cylinder hole machining is finishing, and the processing steps are as follows: milling boss blank surface, drill collar 6 guide hole, drill collar 6 deep hole (depth 175mm), expansion M10*1 bottom hole and chamfering, tapping M10*1 thread , one step processing in place. The drilling time is about one minute, and about 20 cylinders are processed every hour. “The four drills currently used have drilled more than 7,000 holes, and almost one drill can process 1600 to 1800 holes. Compared with another well-known brand previously used, the drill can drill up to 1200~1400 holes, which can be said to have a higher life. After an actual comparison, the advantages of Walter products are highlighted. According to reports, the material of the engine block of Jianghuai Automobile is gray iron 250. Because of the high silicon content, the wear resistance of the tool is extremely high. Therefore, Walter's drill has reached such a high life rate far beyond the industry average. In addition, in addition to reducing the cost of the tool life, it also greatly saves the tool change time, which can be described as two-fold.
Longer life and lower cost
In the selection of milling tools, Jianghuai found the Walter BLAXXTM milling cylinder end face, and the Walter Tiger·tec® tiger blade was used to mill the two end faces on the bearing hole.
The success of the Walter Tiger Blade is obvious to all, and almost no one in the industry knows the power of the Tiger Knife. Over the years, Tiger·tec® cutting tool materials have set new standards in cutting across multiple applications, helping tens of thousands of users achieve increased machining efficiency. Jianghuai Foundry has started to use the tiger knife product in 2012. It is currently used to process the five faces of the cylinder: it can be completed in one time. The processing requirements for all surfaces are roughness Ra 1.6, and the tolerance is controlled within five wires. In this way, to the Jianghuai automobile engine factory, as long as the end face is finished milling, you can enter the next process, and the overall processing cycle is well guaranteed.
Walter BLAXXTM is Walter's new generation of milling cutters introduced in recent years, representing an extremely rugged and extremely precise construction and exceptional performance and process reliability. Walter technical experts said: "The design advantage of the blade is to reduce the cost of the blade. Thanks to the use of the latest compression molding technology, and designed as four spiral positive cutting edges, it can be equipped with different size blades, Different number of cutting edges. The large volume of the core of the tool body ensures the stability during processing, and brings relatively quiet characteristics during processing, which makes the machining process more reliable. Very little vibration makes the tool life increase. In addition, the blade is placed on the periphery and the extension space for more cutting edges can be designed later. It can be said that the black front man perfectly combines the advantages of the blade body and the blade to increase the tool strength, heat resistance and wear resistance. Greatly improved. In addition, the characteristics of the new Tiger·tec® Silver silver tiger blade cutting material are not to be underestimated.â€
“The staff reflects that Heifengxia has a longer life under the same processing efficiency than other imported tools previously used. For example, the previous blade can process 30 cylinders, and now it can process 50~60. The cylinder block, and the seismic resistance of the tool body has been improved very well," said the director.
The most direct manifestation of efficiency gains is a reduction in production costs. "Now the company is increasingly demanding lower manufacturing costs, and we are required to assess the fixed cost. Not only the unit price calculation, but the accounting to each processing step, the challenge is very large." Director said.
Compared with the director, the average cost to the single-piece machining of the engine was about 60 yuan to 100 yuan, but now it costs only 20 yuan, and each piece reduces the cost loss by as little as 40 yuan. If you calculate 100,000 pieces per year, there will be 4 million cost savings. In fact, the fast-growing Jianghuai Automobile has an annual production capacity of 700,000 vehicles, 500,000 engines and related core components. A small process adjustment can reduce the cost by about two-thirds, which is undoubtedly a successful innovation attempt for the group company.
The director finally introduced: “Walter helps us achieve smooth changes in the process through high-performance products and services, which brings us certain economic benefits and sustainable development space. Moreover, they often ask for products actively. The application situation, combined with our own rich experience to give improvement advice, this cooperation is very reassuring. If there are new processing tasks, new processing requirements, we are very willing to try Walter's new products, and are willing to discuss with them A new solution. Indeed, in the provision of processing technology and solutions, Walter has always maintained timely and in-depth communication with customers to understand the real needs of customers in detail. With "advantageous technical capabilities", Walter is continuously helping customers to achieve the upgrade goal of improving processing efficiency and reducing processing costs.
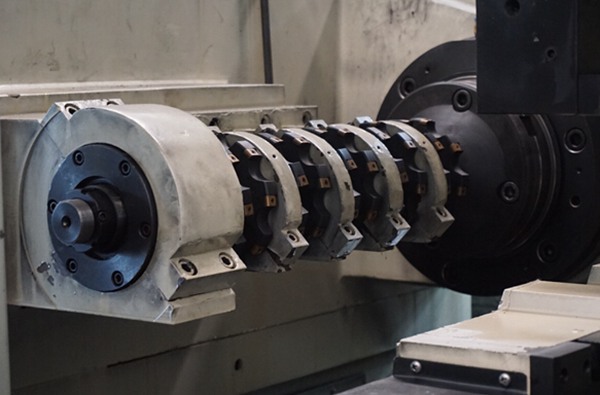
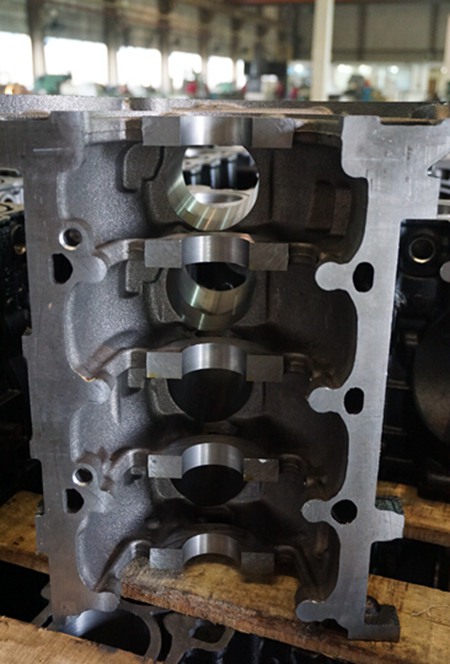
Figure 4. Jianghuai casting uses a tiger knife to machine the five faces of the cylinder: it can be completed in one time. The processing requirements for all surfaces are roughness Ra 1.6, and the tolerance is controlled within five wires, which guarantees the next process. .
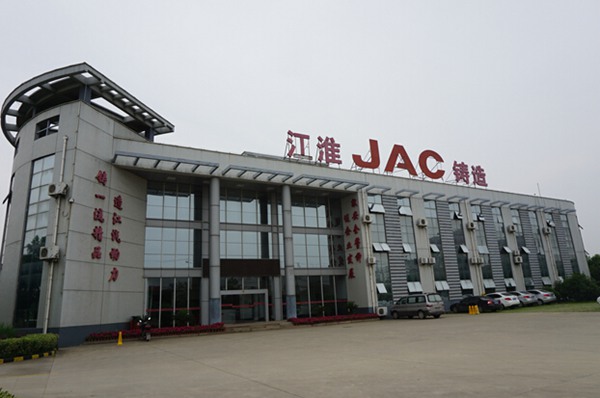
Figure 5. Jianghuai Automobile is the leader among domestic brands. Its core engine 1.5TGDI engine is the first domestically developed model with mature technology and extensive mass production.
Eramic Knife Set,Knife Sets,Boning Knife Set,Bread Knife Set
YANGJIANG TRI-WIN INDUSTRY & TRADE CO.,LTD , https://www.triwintableware.com