Vibration aging treatment is a commonly used method for eliminating internal residual internal stress of engineering materials. It is caused by vibration, so that the vector sum of residual internal stress and additional vibration stress inside the workpiece exceeds the yield strength of the material. The plastic deformation causes the internal stress inside the material to relax and reduce.
Defining vibration aging treatment is a commonly used method for eliminating internal residual internal stress of engineering materials. It is caused by vibration, so that the vector sum of residual internal stress and additional vibration stress inside the workpiece exceeds the yield strength of the material. A small amount of plastic deformation causes the internal stress inside the material to relax and reduce.
Mechanism of vibration aging The essence of vibration aging is to apply a dynamic stress to the workpiece in the form of vibration. When the dynamic stress is superimposed with the residual stress of the workpiece itself, the workpiece will be microscopic or macroscopic when it reaches or exceeds the microscopic yield limit of the material. Local and integral elastic plastic deformation, at the same time reduce and homogenize the residual stress inside the workpiece, and finally achieve the purpose of preventing deformation and cracking of the workpiece and stabilizing the workpiece size and geometric precision.
Simple procedure for vibration aging process
Vibration treatment technology, also known as vibration to eliminate stress, is also called vibration aging in China. It is to place a motor system with an eccentric weight (called an exciter) on the component, and support the component with an elastic object such as a rubber pad. The controller starts the motor and adjusts its rotation speed to make the component resonate. Adjusting the residual stress can be achieved after about 20 to 30 minutes of vibration treatment.
It can be seen that the technique of adjusting residual stress with vibration is very simple and feasible.
Vibration aging process characteristics
The reason why vibration aging can partially replace thermal aging is that the technology has some obvious features.
1. Significant improvement in mechanical properties
The residual stress of the vibrating member can be eliminated by about 20% to 80%, and the high tensile stress region is eliminated more than the low stress region. Therefore, the use strength and fatigue life can be improved, and stress corrosion can be reduced.
It can prevent or reduce the occurrence of micro cracks caused by heat treatment, welding and other processes. It can improve the resistance of components to deformation, stabilize the accuracy of components, and improve mechanical quality.
2. Strong applicability
Because the equipment is simple and easy to move, it can be processed on site at any location. It is not limited by the size and material of the components. Vibration aging technology can be used for components from tens of kilograms to hundreds of tons. Especially when some large components cannot be used for thermal aging treatment, the vibration aging has more outstanding advantages.
3. Save time, energy and expenses
The vibration aging takes only 30 minutes to carry out the next process. The heat aging requires at least one to two days, and requires a large amount of kerosene, electricity and other energy sources. Therefore, compared with thermal aging, vibration aging can save more than 90% of energy, and can save more than 90% of the cost, especially saving huge investment in building large kiln.
Development and application of vibration aging process
The technique of eliminating the residual stress of metal components by vibration was patented in the United States in 1900. However, due to the long-term use of heat aging, and the mechanism of stress relief at the time is not very clear, and the high-speed motor has not yet appeared, resulting in heavy equipment and inconvenient adjustment, this technology has not been developed and applied.
Until the 1960s due to the energy crisis, the United States, Britain, Japan, the Federal Republic of Germany and other countries began to study the mechanism and application process of vibration aging. Especially in the 1970s, due to the emergence of adjustable high-speed motors, the development of vibration-removing stress devices (VSR systems) was promoted: in 1973, the United Kingdom made a portable VSR system, VCM80. Later, Martin Engineering of the United States also developed advanced equipment. LT-100R type VSR system. France and the Soviet Union also produced PSV and NB VSR systems, respectively. These advanced vibration devices promote the development and application of vibration stress relief processes.
According to statistics, there are currently more than 10,000 VSR systems in use in the world. There are more than 700 companies in the United States that use the vibration aging process. The Soviet Union and some countries in Eastern Europe are also using them in large quantities, and they have achieved significant economic benefits. Vibratory aging has been defined in many countries as a standard process that must be used for certain mechanical components. Almost no company in the UK does not use this technology.
Vibration treatment has a wide range of applications in foreign countries, and there are many types of components to be processed. For example: 1. A machine tool company in the UK produces large precision machine tools with a precision of 0.01 mm / 2 m for the bed and column. In the past, the use of thermal aging has poor precision retention, and later changed to vibration aging to meet the accuracy requirements, so the vibration aging has now been defined as the standard process of the product. 2. The precision pump body of aluminum alloy casting produced in the UK is 275×300×150mm, which is also guaranteed by vibration aging. 3. American PX Engineering Company used vibration aging to eliminate the internal stress of the 8-ton welded structure gear to reduce welding cracks. 4. Pont Land Electronics, Inc., USA, uses this technology to process 4 ton forging blanks. The company stipulates that the forgings are subjected to three vibration treatments: (1) after roughing (2) roughing and (3) finishing. The stability of the forging is guaranteed after three treatments. 5. The Washington Steel Company of the United States vibrates the 47-ton shearer seat produced by the company. The shearer seat is welded from 152mm to 203mm thick steel plate with a reinforced rib thickness of 38mm to 76mm. The large and heavy components replace the past thermal aging treatment with only 40 minutes of vibration treatment. 6. Northwest Industrial Corporation has also used vibration aging treatment for 2,800-ton ocean towers and 1280-ton rigs. 7. In the United Kingdom, vibration aging is applied to the onshore wellhead platform, and the wellhead platform is welded into a 6m×6m×2m tubular structure by a steel pipe with a diameter of 200mm. 8. In the British jet engine flame tube lining, cracks occurred due to thermal expansion after welding, and the scrap rate accounted for more than 30%. Later, the vibration aging process was adopted, and the scrap rate was almost zero. 9. All special machine bedes produced in the UK are replaced by vibration aging for thermal aging. More than 30 machine tool factories and more than ten forging equipment factories are the production processes that use vibration aging as a standard.
The United States, Britain and other countries also use vibration aging in other industrial sectors, such as paper machinery factory, ship bearing factory, laser welding machine factory, gear box manufacturing plant, textile machinery factory, steel rolling equipment factory, printing machinery factory, pump manufacturing factory, Oil production equipment plants, power generation equipment plants, boiler plants, etc. all use vibration aging to eliminate the stress of the components. Since 1975, this technology has also been rapidly developed and promoted in China, and has made great breakthroughs in machine tool castings.
For many years, the influence of vibration aging on the fatigue life of welded components has been the focus of great concern and debate among experts at home and abroad. Some units in China have done a lot of research and concluded that vibration aging has a great influence on the mechanical properties of metal materials. A reasonable vibration aging process can improve the fatigue life of welded components. These conclusions lay a theoretical foundation for the application of vibration aging on welded components.
The vibration aging process has been applied in China for more than 20 years, and many companies have applied vibration aging technology to some important basic components. 1. Generator base, end cover, seat ring and hydro-generator vane in large power plant equipment manufactured by Harbin Electric Machinery Factory. 2. Welded structural parts in steel rolling equipment manufactured by China's No. 1 Heavy Machinery Plant, large forged shafts. 3. The combined machine tool bed welding parts produced by Dalian Machine Tool Plant and the CD6140 ordinary lathe casting bed. 4. The Dongfeng 4D diesel locomotive bogie welded components produced by Dalian Locomotive Works of the Ministry of Railways improve the fatigue life and the secondary vibration aging after the rough machining of the diesel engine body by vibration aging to prevent fatigue cracks in the machine during use. 5. In the blast furnace renovation, Anshan Iron and Steel Company has some large-scale metal structures that cannot be aged, such as furnace shells, support rings, vaults, ladle turntables, etc. 6. Large metal structures in major projects in the aerospace industry use vibration to eliminate stress after welding. 7. The products of Dalian Dagong Vibration Aging Technology Co., Ltd. are made of stainless steel "target=_blank> stainless steel welded, can not be heated and aging treatment, using vibration aging, which prevents deformation and improves corrosion resistance. From the overall situation, the vibration aging process has been widely applied and the scope is expanding.
Frequently asked questions about vibration aging processes
Because some users do not understand the mechanism of vibration aging, blindly use some simple (so-called "automatic vibration aging") vibration aging equipment to aging the product. This method, which is completely independent of the individuality of the workpiece and only preset according to the parameters of the manufacturer of the vibration aging equipment, adopts one or several process parameters for aging of various workpieces, which may cause the following conditions to occur in the aging workpiece:
2.1. False aging: the workpiece does not resonate or the amplitude is small or the amplitude is large, but the workpiece as a whole is rigid or vibrating. The “automatic vibration aging equipment†can also print or output various aging parameters and curves according to preset programs. Misleading the operator and the craftsman to judge that the workpiece does not achieve the effect of aging at all;
2.2. False aging: Although the workpiece generates resonance, the vibration mode that occurs is inconsistent with the vibration mode required by the workpiece. The dynamic stress is not added to the part where the workpiece needs to be stressed. This does not make the workpiece achieve the intended aging effect and affect the aging effect.
2.3. Over-aging: Since the reasonable aging parameters are not used for the individuality of the workpiece, the parameters are immersed completely according to the parameters of the blind preset. The resonance may be too strong or the amplitude is too large, resulting in defects inside the workpiece (cracks, slag inclusions, pores). , shrinkage, etc.) continue to expand, tear, and even the serious consequences of retirement.
3. Process analysis of vibration aging: It can be seen from the current situation of the vibration aging process that the aging treatment of the workpiece with the blind automatic vibration aging process is pseudo-scientific, which not only fails to achieve the purpose of the workpiece, but also appears Serious consequences, resulting in cracking of the workpiece, and even the destruction of the machine. So, what kind of vibration aging process is scientific?
First of all, the residual stress distribution of the workpiece, the accuracy of the shape and position, and the future working load and the possible failure reasons should be analyzed before the aging, and a reasonable vibration aging process should be established to determine the aging route and the key aging parts.
3.1. Shape and position accuracy analysis: According to the straightness, cylindricity, flatness, coaxiality, symmetry of the workpiece, etc., different excitation forces should be adopted, and different vibration modes should be selected.
3.2. Resonance frequency analysis: Select different support methods according to workpiece strength, rigidity, batch size or use vibration platform for processing.
3.3. Vibration mode analysis: different frequencies correspond to different vibration modes, and different vibration modes correspond to different dynamic stress fields.
3.4. Working load: For the future working deformation of the workpiece, it is important to eliminate the residual stress of the workpiece load in the working condition state, and select the corresponding vibration mode for aging treatment.
3.5. Failure analysis of working conditions: According to the problems that may arise in the future, different time for different excitation force should be used for aging treatment. Secondly, the vibration aging equipment should be scientifically selected according to the time-dependent workpiece. Some simple, so-called “automatic vibration aging equipment†should not be selected; instead, the vibration aging mechanism should be deeply understood, and such vibration aging equipment should be selected by comparison: a) stable operation, closed-loop speed control, reliable speed, online printing, High cost performance: b) Strong and weak electrical isolation, strong self-protection function, low failure rate, easy maintenance: c) easy to operate, human-machine dialogue, and the ability to set device operating parameters through the panel input password without changing the hardware settings: d) No matter which operating mode (manual, semi-automatic, fully automatic, programming) is used, multi-peak automatic identification, multi-vibration aging can be realized, and partial scanning and partial printing can be realized; and the manual personality can be adopted for the personality of the workpiece. (According to the operator's experience and willingness to complete the pre-vibration scan, print, identification, aging, post-vibration scan), complete the vibration aging of the useful peaks, avoid processing the useless peaks, and also find a large number of process parameters by super manual. Scientific analysis to find commonality of the same parts, quickly and easily on the panel The program is stored and stored so that the automatic processing of the workpiece can be called at any time in the future; e) Remote operation: For large parts, the operator can remotely control the equipment and adjust the operating parameters while touching the workpiece. The whole process of aging; at the same time, it can keep the operator away from noise and protect the operator.
Http://news.chinawj.com.cn Editor: (Hardware Business Network Information Center) http://news.chinawj.com.cn
Single Glass Reactor is a multifunctional reactor, which can be used for various biochemical synthesis reactions under constant temperature conditions, and can also be reflux or distilled at different temperatures.
The machine can be heated by optional heat distribution, and the cooling coil can also be selected.
Characteristic
The glass module is made of high borosilicate glass (GG17) with excellent physical and chemical properties.
Electronic stepless speed regulation, smooth operation, large torque, no spark, long life.
Tetrafluoroethylene module seal, proprietary technology, can ensure good vacuum and long service life.
The overall structure is stable and can be moved as a whole.
Minimum or dead angle PTFE discharge valve can effectively reduce stirring dead angle.
Kettle body and interface can be customized according to customer requirements
Whether refrigeration or heating, we can produce supporting products according to customer requirements.
The overall structure is scientific, the product design is novel, practical and beautiful, leading in the same industry in China.
Installation of cooling coil, heating sleeve and explosion proof device can be installed according to user needs.
Model / Capacity: 1L, 2L, 3L, 5L, 10L, 20L, 30L, 50L, 100L, 150L, 200L.
Other Customizable explosion-proof, cooling coil, etc.
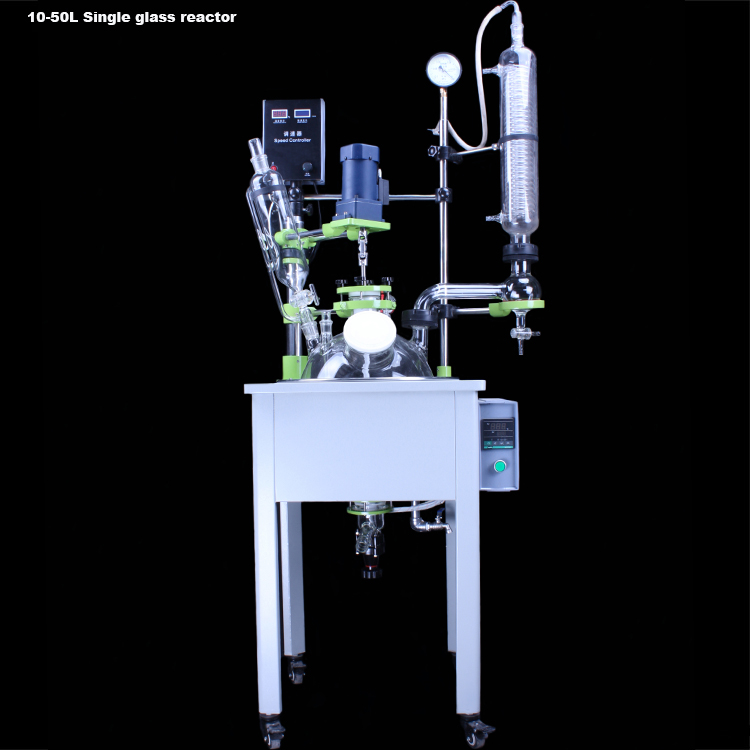
Single Glass Reactor
Single Glass Reactor,Single Layer Glass Reactor,Chemical Single Glass Reactor,Single Layer Reactor,Mini Glass Reactor,Glass Reactor Kettle
Zhengzhou mingyi instrument equipment co.,ltd , https://www.mingyint.com