In the main engine main engine factory and crankshaft parts factory in China, induction hardening has become a major crankshaft strengthening method and is expanding its application. The crankshaft is intensified by induction hardening, and the technical and economic indicators are ideal.
1. Crankshaft induction quenching advantage
(1) After induction hardening + low temperature tempering (or self-heating tempering), the steel crankshaft can increase the fatigue strength of the crankshaft by more than 100% compared with the tempered state, and greatly improve the wear resistance of the journal surface (quenching + back) The fire hardness can be precisely controlled at 50 to 55 HRC), while other reinforcement methods are difficult to achieve both of the above indicators.
(2) Induction quenching has high production efficiency, and induction quenching is clean and can be produced according to the beat. It can be arranged directly on the crankshaft production line to save logistics costs and time.
(3) Only the crankshaft heats the surface portion that needs quenching and hardening such as the journal, and the electric efficiency is high and the time is short, which is more than 80% lower than other heat treatment energy.
(4) Since the heating range is small and the time is short, the processed crankshaft has small deformation and less oxidative decarburization, which can reduce the finishing allowance and reduce the machining workload.
2. Induction hardened crankshaft material
(1) Crankshaft materials Common materials for automobile crankshafts include quenched and tempered steel 42CrMo, 35CrMo, 40Cr, 40MnB, etc., non-tempered steel 48MnV, etc., as well as ductile iron. The alloy composition of Cr and Mo in the material can significantly improve the hardenability of the material, thereby increasing the strength of the crankshaft, but the price is higher, and the quenching cracking tendency is large, and a suitable quenching cooling medium is needed to avoid the quenching crack, so when selecting materials The spheroidal graphite cast iron and non-quenched and tempered steel should be preferentially selected to meet the performance requirements to reduce production costs. As long as the tooling is suitable, the process is reasonable, and the operation is accurate, whether it is non-tempered steel or ductile iron crankshaft, induction hardening can achieve technical requirements.
(2) Pre-heat treatment of roughened steel The quenched and tempered steel can obtain fine and uniform structure, and the internal stress of the part is small, which is very beneficial to induction quenching: uniform quenching structure, small quenching deformation and cracking tendency. Non-quenched and tempered steel uses V, Ti and other elements to refine the grains, which greatly reduces the production cost while improving various mechanical properties, but it is different from the quenched and tempered steel in the preparation of the structure, so when the induction heat treatment process is formulated It should be analyzed according to its organizational characteristics.
The pretreatment structure of the ductile iron crankshaft mainly includes two types: normalized state and as-cast state. The normalizing treatment can increase the content of pearlite, eliminate the casting stress, and the structure is relatively uniform, and then obtain the hardened layer with uniform structure and hardness by induction hardening. As cast spheroidal graphite cast iron, the pearlite content in the as-cast microstructure is generally 75%-85%, and there are many ferrites. To obtain the ideal quenching structure, the induction quenching process is required. Therefore, the effect of different preliminary heat treatments on induction hardening should be considered when formulating the process.
3. Heat treatment specification for induction hardening
(1) The induction quenching process is formulated to achieve the desired results, and is related to heating power, workpiece material, control gap, heating time, cooling time, workpiece waste heat, quenching cooling medium concentration and pressure. Different parameters should be used for different materials. For example, the toughness of alloy steel is good, suitable for high power heating and rapid cooling, while ductile iron is brittle material, not suitable for high power, long time heating and quenching, heating time and cooling time should be According to the actual conditions of the field equipment, the requirements of the hardened layer of the workpiece. The process parameters of medium frequency induction hardening of alloy steel and ductile iron crankshaft are shown in Table 1, for reference only.
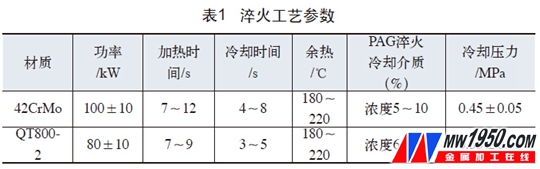
(2) Technical requirements for induction hardening include: surface hardness, hardened zone range, hardened layer depth, metallographic structure, quenching deformation and quenching crack. Metallographic structure of quench hardened layer: steel crankshaft is acicular or fine needle-like tempered martensite, free ferrite should not appear; ductile iron crankshaft allows a small amount of undissolved ferrite in the vicinity of spheroidal graphite, but can not be ring. The depth of the hardened layer and the surface hardness are important indicators for obtaining high fatigue strength, and each has an optimum range. Too high and too low both reduce the fatigue strength. If the depth of the hardened layer is too shallow and the surface hardness is too low, the strength of the part is insufficient and the wear resistance is lowered. Conversely, when the depth of the hardened layer is too deep, the peak of the compressive stress is pushed inward from the surface, and the surface compressive stress is lowered, so that the strength is lowered. The hazard caused by excessive hardness is obvious, which increases the brittleness of the part and severely reduces the strength of the crankshaft under the bending and torsional fatigue load and impact force. The relationship between the depth of the quench hardened layer and the surface hardness and fatigue strength of a common steel crankshaft is shown in Fig. 1.
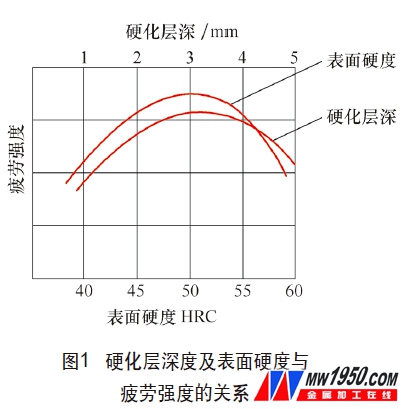
The optimum depth range of the hardened layer shown in the figure is applicable to the φ55 to φ90 mm journal, and the other journals should be adjusted on this basis. When the wear resistance is mainly used, the surface hardness can be as high as 55HRC; while the ductile iron has good self-lubricating property and oil storage capacity, the surface hardness of the crankshaft is ≥45HRC, which has sufficient wear resistance; the fatigue strength is high. At the time, it is necessary to obtain a high and uniform surface compressive stress, and the surface hardness is not excessively pursued.
(3) After induction quenching after quenching, the surface structure is transformed from pearlite to martensite, resulting in residual thermal stress and microstructure stress in the workpiece. The workpiece must be tempered in time, generally within 4-8 hours. Otherwise, it will cause cracking of the crankshaft surface.
4. Induction hardening operation essentials
(1) The surface of the part to be treated shall be free from cracks, defects, burrs, oil stains and decarburization layers, etc. Otherwise, defects such as quenching cracks, burned parts and insufficient hardness may occur after quenching.
(2) When designing, manufacturing or selecting an inductor, its structural shape and size should meet the process requirements.
(3) During the processing, the sensor and the workpiece should maintain a proper relative position, and the control gap is 1.5 to 2.5 mm.
(4) Correctly select the electrical parameters to make the equipment in the best working condition. The steel crankshaft has a power selection of (100 ± 5) kW and a ductile iron crankshaft selection of (75 ± 5) kW. Steel crankshafts can be treated with higher power, because of their good ductility, suitable for quenching; ductile iron is a brittle material, suitable for lower power quenching, otherwise it is particularly prone to quench cracks.
(5) The measurement of the surface temperature of the workpiece is very important. The photoelectric pyrometer or infrared radiation thermometer should be used to continuously control and control the workpiece blanking temperature, maintain the residual heat at 150-220 °C, adjust the working parameters of the equipment in time, and use the residual heat to realize the workpiece. Self-tempering, this is also a key measure to prevent quench cracking.
(6) According to the material, the shape and size of the workpiece, and the heating method and the required depth of the hardened layer, the cooling parameters, including the cooling method, the quenching cooling medium and the cooling time, are reasonably determined.
(7) The rounded corners of the ductile iron crankshaft are not suitable for quenching and strengthening. The hardened layer should be 3~6mm away from the rounded corners, so that the residual tensile stress at the junction of the hardened zone and the non-hardened zone is far from the rounded corners to improve the fatigue strength and prevent the rounded corners. Excessive stress concentration causes early non-fatigue fracture.
5. Application
Induction hardening and rounded rolling of ductile iron crankshafts are used by more and more crankshaft manufacturers. The rational use of the composite strengthening process will increase the fatigue strength of the crankshaft and greatly improve the surface roughness and wear resistance. Maneuverability.
The following is an example of a medium-frequency induction hardening treatment of a QT800-3 four-cylinder crankshaft of a certain type, which is superior to other surface heat treatments.
(1) Processing flow Iron casting → normalizing treatment → high temperature to tempering → rough processing → primary flaw detection → induction quenching → medium temperature tempering → secondary flaw detection (detection of quenching cracks) → finishing.
(2) Process specification for induction hardening According to the technical requirements of induction hardening of crankshaft, as shown in Fig. 2, the process parameters of induction hardening are established, as shown in Table 2.
(3) Equipment and tooling equipment are semi-automatic quenching equipment for crankshaft, thyristor intermediate frequency power supply, saddle-shaped inductor, concentration 5%~8% PAG quenching liquid.
(4) Test results after treatment After the crankshaft quenching treatment, the hardened layer of each journal is 3.0-4.0 mm, the surface hardness after quenching + tempering is 45-52HRC, and the distance between the hardened area and the side is 5-6.5 mm, quenching Hard metallographic microstructure martensite 6 to 7 grade, no quenching crack; quenching + tempering radial circular runout ≤ 0.5mm (measuring intermediate spindle neck), to meet technical requirements.
6. Conclusion
The crankshaft is one of the most ideal applications for induction heat treatment technology. The performance of the crankshaft after induction hardening is greatly improved, which is beneficial to improve engine performance and greatly reduce production cost. Induction hardening technology is increasingly used in the production of high-end crankshaft products. At the same time, there are many key factors affecting the quality of quenching, such as equipment, tooling, materials, process parameters, etc., timely maintenance of equipment tooling, optimization of process plan, process supervision, etc., which can effectively control the quality of quenching with the constant demand of high-power engines. Increased, crankshaft induction hardening technology will be used in a wider range of applications, and crankshaft manufacturers will also get good returns.
About the author: Zhang Liping, Zhang Xueqiang, Li Yongzhen, Binzhou Haide Crankshaft Co., Ltd.
Horizon Hot tub spas has got below unique technology in the world:
1. Never bubble on spa acrylic shell :
1) You can test our spa shell on 100 degree hot water more than 200 hours and not any bubble on the spa shell, USA spa shell tested in 80 degree hot water not more than 40 hours only.
2)If the spa acrylic shell bubble happen within warranty term, We will free one new spa for you.
2.Horizon Perfect-core spa control therapy system is designed by our company's oversea designer team, It own many unique technology.
1)Total water-proof spa control panel:
You can drip the spa control panel into the water and not any problem.
2). The Extra-pure water treatment system:
This water treatment system can keep the water clear in the spa more than one year without any chemical chlorine.
3.Luxury polymer spa skirt panel:
1)Don`t fade spa skirt panel used outdoor more than 10 years.
We product our spa spa skirt panel with our unique materials which exploited by our engineer team, So our spa skirt can be used more than 10 years, and the color in the skirt will be not lost.
2)Patent Colorful dream skirt
Spa for 4-6 Adults
Hotel Hot tub, 4 persons Hot tub, Family jacuzzi tub,5 persons hot tub, 6 persons spa tub, spa for 4-6 adults, 4-6adults spa tub, party spa tub
Dongguan Horizon Technology Development Co., Ltd. , http://www.horizontub.com